Understanding the Challenge of Scale in Industrial Systems
For the last 37 years, ETI has been in the business of working with industrial water treatment companies to stop scale formation in industrial facilities that rely on water-based systems. Whether it’s boilers, heat exchangers, cooling towers, or piping networks, scale build-up caused by calcium, magnesium, and silica can significantly reduce heat transfer, restrict flow, and eventually lead to unplanned downtime and equipment failure.
In industries where system uptime and thermal efficiency are mission-critical, even minor scale deposits can drive up fuel consumption, cause localized overheating, and increase maintenance frequency. Scale not only disrupts optimal performance-it directly impacts the bottom line.
That’s where descaling plays a critical role. Instead of relying solely on mechanical cleaning or reactive maintenance, descaling chemicals-often referred to as scale removers-are formulated to dissolve and eliminate mineral buildup safely and efficiently. But not all products are created equal. Understanding the chemistry behind descalers, how they interact with other surfaces, and what type of scale they’re formulated to remove is essential to choosing the right solution for your system.
What Is Chemical Descaling?
This is the process of applying acidic or specialty-formulated chemical solutions to loosen and dissolve scale deposits inside equipment and distribution lines. These formulations work by breaking down the bonds that hold sparingly soluble salts–like calcium carbonate, magnesium hydroxide, or silica-together, allowing them to be flushed out of the system.
The most common applications for scale removers include:
- Boilers
- Heat exchangers
- Cooling towers and chillers
- Condensers
- Process tubing and piping systems
In these environments, scale removal helps:
- Restore proper water flow
- Improve energy efficiency
- Extend the lifespan of critical assets
- Reduce cleaning frequencies and labor costs
How to Know When Descaling Is Needed
Scale doesn’t form overnight-but it does build up quickly under the right conditions. Indicators that it’s time for descaling include:
- Reduced system pressure or flow
- Poor heat transfer performance
- Rising energy or fuel costs
- Visible buildup on open piping or tubing
- Frequent need for mechanical cleaning
- Audible “kettling” in boilers or heat exchangers
In many cases, operators notice performance degradation before they visually confirm scale-and by then, the impact on efficiency is already substantial.
Why Scale Type and System Surface Matter
Not all scale is created equal. For example:
- Calcium carbonate is common in hard water areas and forms dense, white crusts.
- Silica forms stubborn, glassy deposits that require specialty formulations.
- Iron and rust-based scale may require dual-action cleaners that target oxidized surfaces.
Equally important is understanding what surfaces you’re cleaning. A product safe for steel tubing may not be appropriate for copper, aluminum, or other surfaces. Some descalers are acidic and highly effective, while others use non-corrosive or buffered formulas designed to protect sensitive materials.
ETI’s water scale remover lineup includes both biodegradable and low-corrosion options, formulated to work across a variety of equipment types, temperature ranges, and system chemistries.
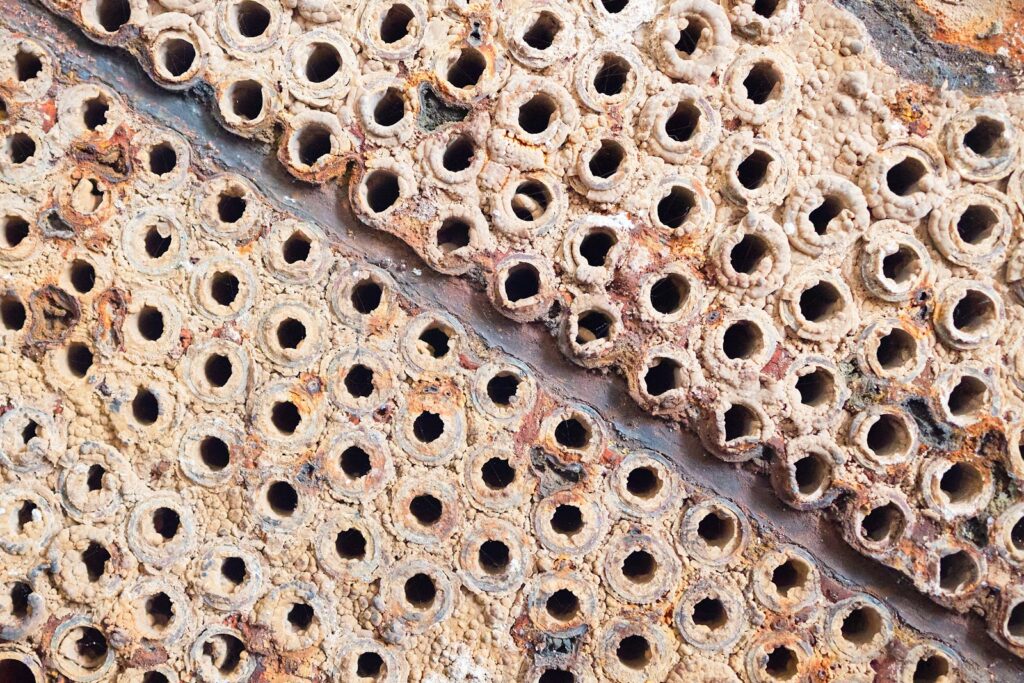
Choosing the Right Scale Remover: What to Look For
When selecting a scale remover for your facility, there’s more at stake than just eliminating deposits. The wrong formulation can damage equipment, introduce unnecessary safety risks, or underperform-leaving systems partially fouled and operators frustrated. Choosing the right chemical descaling solution means balancing cleaning power, material compatibility, ease of use, and safety.
Here’s what to evaluate before placing an order or opening a drum:
1. Know the Type of Scale You’re Dealing With
Different scale deposits require different chemical strategies. For example:
- Calcium carbonate is common in heat transfer systems and responds well to acid-based descalers.
- Silica requires more advanced formulations with chelating agents or specialty blends that loosen hard, glassy buildup.
- Iron oxide or rust scale may need dual-action formulations that dissolve mineral deposits while targeting oxidized metal fouling.
ETI’s scale remover products are available in multiple formulations, including low-corrosion blends for sensitive surfaces and high-strength options for heavily scaled systems.
2. Match the Product to Your System Materials
Some descalers are highly effective at dissolving mineral buildup but can corrode metal surfaces like aluminum or stainless steel. Others are safe on sensitive materials but may be too mild for high-scale loads.
Before you apply any scale removal product, make sure it’s compatible with system metals and elastomers, temperatures, and flow rates.
3. Consider Application Method and Downtime
Some scale removal chemicals are designed for recirculation cleaning-they’re added to the system and pumped in a loop. Others are more effective as soak treatments or may require multiple cycles.
Choosing a product that fits your operation’s cleaning window, manpower availability, and process flow is just as important as choosing the right chemical.
4. Prioritize Safety-For Operators and Equipment
All chemical descalers should be handled with care-but some are significantly safer to work with than others. ETI works closely with operators to ensure not only product performance-but also safety protocols, operator training, and post-cleaning system evaluation.
How ETI Helps You Get Descaling Right
At ETI, we take a formulation-first approach to scale removal. That means we don’t just sell a product-we match the right chemical solution to your equipment, your scale profile, and your operations.
Our services include:
- System assessment – We evaluate the type, location, and severity of your scale buildup
- Product recommendation – From rapid descalers to specialty blends, we tailor the chemistry
- Support for application – We guide dosing, safety, and post-cleaning evaluation
- Ongoing optimization – We help develop long-term strategies
We’ve supported customers in power generation, food processing, metals, and manufacturing-each with different scale profiles, water chemistries, and operational requirements.
Descaling Shouldn’t Be Guesswork
Whether you’re dealing with calcium carbonate in a boiler, silica in a cooling tower, or rust deposits in steel piping, scale is a constant threat to performance. Choosing the right descaling product makes all the difference between a quick system recovery and recurring efficiency loss.
Need Help Choosing a Scale Remover?
Talk to an expert at ETI. We’ll review your system, assess your scale challenge, and recommend the right solution.