Boiler systems demand high-purity water to function efficiently and avoid performance-degrading issues like scaling, corrosion, and pH instability. However, most feed water sources contain impurities that, if left untreated, can shorten boiler internal equipment lifespan, reduce heat transfer efficiency, and increase operational costs. While traditional treatment programs often rely on multiple separate chemicals, an all-in-one boiler feed water treatment package integrates multiple treatment functions into a single formulation. This ensures complete protection, simplifies dosing, and improves overall system reliability.
At ETI, we specialize in precision-formulated chemical blends tailored for boiler system optimization. Unlike traditional water treatment chemical blenders, we focus on custom chemical blending for our partner water treatment companies, ensuring that treatment professionals have formulations engineered for their specific operating conditions. By incorporating multiple treatment components into a single blend, we help facilities improve heat transfer, control corrosion, and extend equipment life.
Key Takeaways
- An all-in-one boiler treatment package integrates key components like oxygen scavenging, scale inhibitors, and amines to optimize efficiency and reduce operational costs.
- Proper monitoring of cycles of concentration, condensate return, and key water parameters by a licensed, certified water treatment partner ensures long-term system protection and performance.
- ETI specializes in customized chemical blending solutions that enhance heat transfer, prevent scaling, and extend equipment life across various boiler applications.
Understanding Boiler Chemical Water Treatment Needs
Industrial boilers power essential industries across the U.S., supplying steam for hospitals, schools, pharmaceutical production, food processing, and manufacturing. In these settings, any disruption to steam boiler systems caused by corrosion, scaling, or water chemistry imbalance can have serious consequences—affecting patient care, disrupting supply chains, or halting production.
To ensure uninterrupted operation, boiler feedwater must have internal treatment to remove dissolved carbon dioxide and oxygen, control scale formation, and stabilize pH. Corrosion, particularly oxygen pitting, is a major threat in high-temperature areas like water walls and superheater tubes, leading to metal failure and costly repairs and downtime. Scaling, on the other hand, reduces heat transfer efficiency and drives up energy consumption.
A strategically formulated chemical treatment program prevents these issues by optimizing feedwater quality, extending equipment lifespan, and reducing excessive blowdown. Understanding the unique demands of each boiler system allows water treatment professionals and their facility clients to fine-tune boiler chemical treatment dosages and formulations, ensuring reliable performance in industries where steam availability is mission-critical.
Key Components of an All-in-One Boiler Treatment
A well-formulated boiler treatment package combines multiple chemicals to prevent corrosion, scaling, and condensate system damage. These treatments are blended into a concentrated, aqueous solution and dosed into the steam system to maintain efficiency and longevity.
Oxygen Scavengers
Dissolved oxygen is a major contributor to boiler system corrosion, particularly in high-temperature areas. While mechanical deaeration removes most oxygen, chemical scavengers are necessary to eliminate residual traces.
- Sodium sulfite reacts with oxygen to form non-corrosive byproducts, protecting metal surfaces.
- Erythorbic acid is a food-grade alternative for applications requiring minimal sulfate contamination.
- Hydrazine, once widely used, is now restricted in many industries due to environmental and safety concerns.
By incorporating the right oxygen scavenger into an all-in-one formulation, ETI chemicals help facilities and our water treatment partners ensure long-term corrosion protection while maintaining compliance with regulatory guidelines.
Amines
Amines neutralize acidic condensate and protect return lines from corrosion. In an all-in-one treatment, a balanced amine blend maintains pH stability throughout the whole condensate piping system.
- Neutralizing amines (morpholine, cyclohexylamine, diethylaminoethanol – otherwise known as DEAE) adjust pH by neutralizing carbonic acid.
- Filming amines (octadecylamine) can create a protective layer on metal surfaces, preventing direct exposure to corrosive condensate.
Amines must be carefully selected based on steam system pressure, condensate return percentage, and pH stability requirements. ETI’s custom formulations ensure optimal amine performance across various operating conditions.
Anti-Scaling Agents
Scale formation is a leading cause of boiler inefficiency and increased fuel consumption. A well-balanced anti-scaling program prevents scale buildup and mineral precipitation while dispersing existing deposits.
- Polymer dispersants (polyacrylate, polymethacrylate) prevent scale formation by keeping dissolved solids in suspension.
- Phosphates precipitate calcium and magnesium, allowing them to be removed through blowdown.
- Chelating agents bind to metal ions, preventing them from forming scale deposits.
By incorporating these scale inhibitors into a single formulation, ETI provides superior water chemistry and scale control, while reducing the need for frequent manual adjustments.
Formulating the Right Combination
Crafting the ideal blend of raw materials for boiler water treatment chemicals is a complex endeavor that combines technical know-how, experience, and precision. The treatment process utilizing these chemicals follows a systematic approach based on key parameters such as cycles of concentration (COC), condensate return, and chemical dosing requirements. COC is determined by comparing makeup water TDS (total dissolved solids) to boiler water TDS, indicating how efficiently water is being reused before blowdown.
To manage pH, corrosion, and scaling, chemical dosages should be carefully calculated based on system volume and the feedwater chemistry characteristics. Chemical dosing is typically measured in parts per million (ppm), mg/L, or pounds per 1,000 gallons, allowing for greater control over treatment effectiveness. Additionally, iron levels and CO₂ concentrations can serve as key indicators of corrosion activity in boiler systems.
TABLE 1
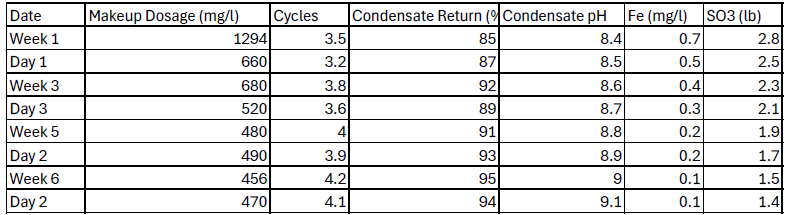
The above data represents a sample scenario where a 250 HP boiler operating in a small manufacturing plant faced common challenges of low condensate pH, moderate CO₂ levels, and fluctuating condensate return. Initially, the system showed a pH of 6.0, which posed a risk of return-line corrosion, while condensate return was only 30%. Through a targeted chemical treatment program, the pH steadily increased to 7.6, ensuring better metal protection, while CO₂ levels dropped from 12 mg/l to 3.5 mg/l, minimizing carbonic acid corrosion. The cycles of concentration improved from 6.5 to 8.0, reflecting more efficient water use, and iron levels fell from 0.8 mg/l to 0.2 mg/l, confirming improved corrosion control.
By week six, the system had stabilized with higher condensate return (62%) and consistent chemical dosing. The program successfully optimized sulfite levels, enhanced system efficiency, and reduced overall chemical consumption for the client, leading to lower operating costs and extended equipment life. With proper water chemistry management, this facility’s boiler now operates with improved reliability, reducing downtime and maintenance concerns for the manufacturing facility.
Interpreting Boiler Water Treatment Performance Data
Cycles of Concentration and Condensate Return
One of the primary goals of boiler water treatment is to maximize cycles of concentration while ensuring efficient condensate return. Increasing cycles allows for better water utilization, reducing the need for excessive blowdown.
Metric | Starting Value | Final Value | Key Change |
Cycles of Concentration | 6.5 | 8.0 | Improved efficiency in water use |
Condensate Return (%) | 30% | 62% | More steam is recovered, reducing makeup water demand |
An improvement in cycles of concentration from 6.5 to 8.0 reflects better water conservation and reduced blowdown losses. A higher condensate return rate (from 30% to 62%) means more steam is being recovered instead of lost, reducing the need for fresh makeup water and excess chemical dosing.
pH Stability and Corrosion Control
Condensate system corrosion is influenced by factors such as CO₂ concentration and pH stability. Proper chemical dosing ensures pH remains within the ideal range, minimizing corrosion risks.
Metric | Starting Value | Final Value | Key Change |
Condensate pH | 6.0 | 7.6 | Improved protection against acidic corrosion |
CO₂ (mg/L) | 12 | 3.5 | Lowered carbonic acid formation, reducing metal degradation |
Iron (Fe) (mg/L) | 0.7 | 0.1 | Reduced corrosion, confirming effective treatment |
The increase in pH from 6.0 to 7.6 demonstrates how a properly formulated treatment neutralizes acidic conditions in the return system, preventing carbonic acid corrosion in steam lines. The CO₂ concentration drop from 12 mg/L to 3.5 mg/L further reduces corrosion risks, while the decrease in the iron oxide levels (0.7 mg/L to 0.1 mg/L) confirms a reduction in system corrosion.
Sulfite Levels and Oxygen Scavenging Efficiency
Sulfite-based oxygen scavengers play a crucial role in boiler efficiency by preventing oxygen pitting and metal failure in boilers. The following data shows how optimizing sulfite dosage improves system efficiency.
Metric | Starting Value | Final Value | Key Change |
SO₃ (lb) | 2.8 | 1.4 | Reduced oxygen scavenger demand |
A reduction in SO₃ levels from 2.8 lb to 1.4 lb suggests that the system required less sulfite over time, meaning oxygen ingress was minimized and scavenger consumption was optimized. This reflects a properly sealed system with lower oxygen intrusion, resulting in more stable chemical consumption.
Why Choose an All-in-One Boiler Chemical Treatment Package?
A well-designed, all-in-one boiler treatment package simplifies chemical management while enhancing system efficiency. By integrating key treatment components—oxygen scavengers, scale corrosion inhibitors, and condensate system protectants – water treatment providers can expect simplified dosing, optimum performance, reduced chemical waste, and lower overall costs.
Beyond cost savings, a consolidated treatment approach ensures consistent protection across all boiler components, minimizing unexpected maintenance costs, downtime, and performance fluctuations. Instead of managing multiple chemicals with varying compatibility, facilities and water treaters can rely on a single, optimized blend tailored for reliability and long-term system performance.
Why ETI’s Chemical Blending Expertise Stands Out
ETI specializes in precision-formulated boiler treatments that optimize cycles, enhance heat transfer, and protect critical components in low, medium, and high-pressure boilers. Our portfolio includes pre-op cleaners, online descalers, passivators, and cycle-optimized treatments designed for systems ranging from ultra-pure to high-hardness water environments. With advanced antiscalant and polymer technologies, many of our blends are also FDA- and USDA-approved for regulated industries.
What sets ETI apart is our application-driven and water treatment-centric approach. We formulate chemical solutions that align with your system’s specific water chemistry and operational needs. Our training and certification programs ensure water treatment specialists have the expertise to implement our formulations effectively. With decades of experience in custom chemical blending, ETI remains a trusted partner for water treatment professionals seeking innovative, high-performance solutions across the country.
Take the Next Step with ETI
If you’re looking for high-performance, cost-effective boiler treatment solutions, ETI’s chemical blending expertise ensures the best possible formulation for your system.
Contact our team today to develop a tailored treatment program that meets your facility’s exact water treatment needs.
Frequently Asked Questions (FAQs)
1. Why is an all-in-one boiler treatment better for most boiler systems than separate chemical treatments?
An all-in-one package ensures chemical compatibility, simplifies dosing, reduces waste, and improves overall system performance compared to using multiple individual treatments.
2. How do oxygen scavengers protect boiler systems?
Oxygen scavengers eliminate dissolved oxygen from boiler tubes, preventing corrosion and oxygen pitting in high-temperature areas like water walls and superheater tubes.
3. What role do amines play in boiler treatment?
Amines adjust pH levels in boiler and condensate system systems, protecting steam return lines from corrosion and ensuring balanced water chemistry.
4. How can I tell if my boiler water treatment chemicals are working effectively?
Regular testing of pH, iron levels, sulfite levels, CO₂ concentrations, and condensate return rates confirms treatment effectiveness and helps fine-tune chemical dosages.
5. How does ETI’s approach differ from standard chemical suppliers?
ETI provides custom-blended solutions tailored to specific system conditions, ensuring optimized chemical performance, cost efficiency, and regulatory compliance across various industries.