In industrial water treatment, your chemical program should be an asset, not a budgetary black hole. Yet too often, the ETI team and it’s partners see facilities throwing money at chemical solutions that don’t match their water profile, are over-applied, or worse, cause downstream problems like fouling, corrosion, or excess sludge. It results in inflated operating costs, frustrated maintenance teams, and no real improvement in system performance.
The truth is that a thoughtfully formulated chemical treatment program does more than just protect your heat exchangers and keep your towers clean. It eases operations, reduces chemical consumption, cuts down on hauling costs, and helps you stay ahead of environmental regulations. That’s real cost optimization – not just buying cheaper product, but designing smarter solutions.
At ETI, we’ve spent nearly four decades helping water treatment professionals fine-tune their programs for maximum efficiency and performance. In this article, we’re digging into the strategies behind a cost-effective chemical water treatment program.
Understand Your Water’s Chemistry Before You Treat It
You can’t optimize a chemical treatment program without first understanding what you’re up against. Every system, from boiler feedwater to cooling towers to industrial wastewater, starts with a unique water profile. Treating it blindly or using off-the-shelf formulas is a fast way to overspend, underperform, or both.
Water may look the same coming out of a pipe, but its composition tells the real story. Questions like:
- What’s the pH?
- Are you dealing with high levels of suspended solids or very fine particles?
- What’s the mineral content, especially things like sodium ions, calcium, iron, or silica?
- Is it loaded with organic compounds or prone to biological activity?
…determine what kind of chemical treatment or chemical wastewater treatment you actually need.
With proper testing and analysis, whether you’re dealing with industrial wastewater treatment or preparing water for reuse, a deep dive into your wastewater composition helps pinpoint the right approach. Tools like lab analysis, on-site meters, and even ion exchange modeling can provide clarity. Once you know what you’re treating, you can select chemicals that target the right reactions, without waste.
For example, if your influent contains high levels of sodium and organics, dosing sodium-based alkalinity boosters like sodium hydroxide may push your system out of balance. Or if you’re seeing turbidity from very fine particulates, you might need a specific coagulant, rather than increasing polymer dosage and hoping for the best.
Build a Program That Does More With Less
One of the biggest mistakes we see in water treatment is throwing multiple single-purpose chemicals at a problem instead of using smarter, multi-functional water treatment blends. Not only does that drive up your chemical treatment costs, but it clutters your program with unnecessary complexity. More drums, more freight, more room for error.
The better way is to design a program that works harder with fewer products. At ETI, we specialize in formulating blended chemistries that can provide a single, high-performing water treatment solution. That means fewer deliveries, less chemical handling, and simpler training for your team.
It’s about optimizing the chemical treatment reactions themselves. When your products are engineered to work together rather than layered on top of each other, you get more reliable water treatment, fewer side reactions, and better system protection. That’s the difference between applying chemistry and designing a chemical process.
In a cooling tower plagued by scale and fouling, a typical approach might involve a cocktail of acids, biocides, and dispersants. But with a carefully formulated blend that includes a threshold inhibitor, sequestrant, and bio-stabilizer in the right ratios, you can control scaling, corrosion, and microbial growth with a single feed point. Less product, better control.
Wastewater Treatment That Doesn’t Waste Money
Wastewater treatment is one of the biggest hidden costs in industrial operations, and one of the easiest places to bleed money if your chemical program (or biological wastewater treatment program) isn’t dialed in. Whether you’re dealing with process water, cooling tower blowdown, or complex wastewater streams, treating it right means matching the chemistry to the load, not just ticking a box for compliance.
Too often, facilities rely on generic chemical wastewater treatment programs that aren’t tailored to the actual makeup of their influent or discharge. The result? Overdosing, underperformance, and sky-high hauling or surcharge costs. Smart programs take a different approach – starting with wastewater characterization and choosing chemicals that are fit for the job.
Match Chemical Treatment to the Problem
If you’re looking to remove heavy metals, suspended solids, or phosphate, chemical precipitation may be your best tool, assuming you’re using the right coagulant and applying it under the correct pH conditions. Get that wrong, and you’re generating excess sludge or missing your permit limits entirely.
For oxidation of stubborn contaminants or odor control, oxidizers like hydrogen peroxide and sodium hypochlorite are workhorses when used appropriately. But they can also drive up costs if misapplied. Overdosing within a water treatment process means more chemical wasted and higher residuals to neutralize downstream.
On the other hand, for disinfection – chlorine dioxide offers a powerful, targeted kill without the dangerous byproducts of traditional chlorine, especially in systems where biofilms or resistant organisms are a concern. Plus, it breaks down safely, which can cut your chemical neutralization costs.
Smarter Integration = Lower Costs
The most common approach – pairing biological wastewater treatment with chemical polishing – lets the bugs do the heavy lifting, then brings in the right chemistry to fine-tune discharge quality. It’s a proven method for reducing both chemical spend and sludge volumes.
Whether you’re discharging to POTW, reusing internally, or zeroing in on water recovery, the goal is the same: treat with precision. When your chemistry is tailored to the wastewater treatment and system demand, you get more value from every drum and fewer surprises on your utility bill.
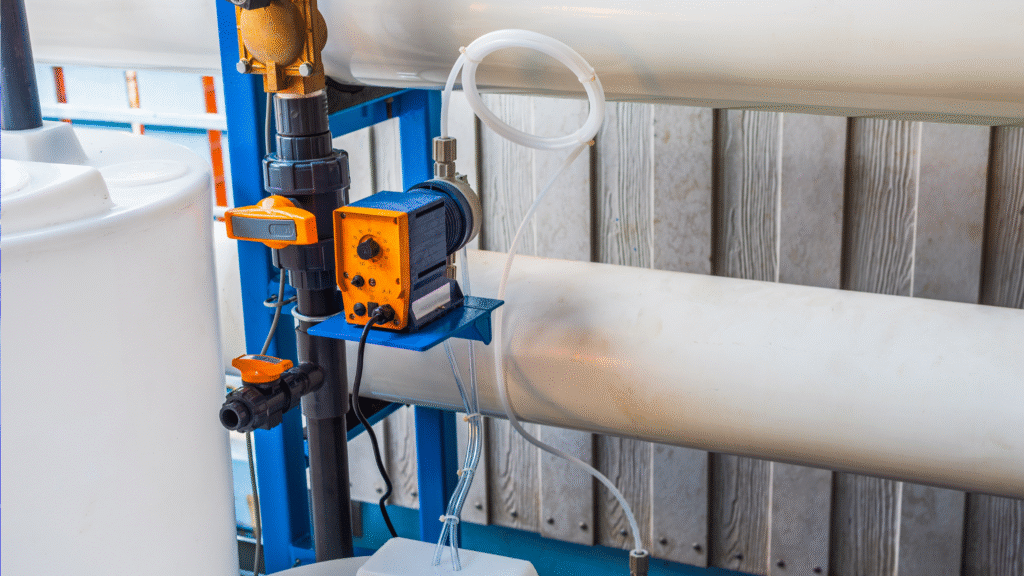
Mind the Operational Side: Equipment, Dosing, and Monitoring
Even the best-formulated chemistry can fall flat if your application methods are off. Poor dosing practices and outdated feed systems don’t just hurt performance but also waste money every single day. That’s why smart chemical program design goes hand-in-hand with smart operations.
Dosing: Get It Right, Get It Consistent
Too many facilities run on “set it and forget it” dosing. But water conditions change – whether it’s temperature shifts, flow rate fluctuations, or variability in incoming water quality. If you’re dosing based on yesterday’s numbers, you’re probably overdosing today.
That means wasted product, unnecessary system stress, and in some cases, non-compliance.
Investing in automated dosing systems and real-time monitoring tools can help you dial in precise chemical feed based on actual system demand. From cooling towers to closed loops to industrial processes or drinking water, dosing should be dynamic, not static.
Equipment Calibration Makes a Difference
Pump performance drifts. Sensors wear out. Controllers lose accuracy. If you’re not regularly calibrating feed systems, especially those handling high-impact products like sodium hydroxide, you’re likely wasting chemical and throwing off your treatment balance.
Even small improvements in feed accuracy can drive significant cost savings across a large industrial operation. ETI routinely helps clients identify these “leaks” in chemical usage and tightens the program to reduce waste without risking performance.
Align Chemistry With System Design
Not all equipment handles chemicals the same way. Certain materials of construction react poorly with oxidizers like sodium hypochlorite. Some dispersants lose efficiency if shear rates are too high. We consider these variables during formulation to ensure every product is compatible with your specific system, not just in theory, but in practice.
Smart chemical programs don’t end with the drum. They extend all the way through your system, right down to the metering pump and control panel.
Smart Chemistry for Safer Drinking Water and Reuse
Optimizing your chemical program is about doing more with the water you already have. Whether you’re treating for discharge, reuse, or even drinking water, well-designed chemistry plays a critical role in turning compliance into opportunity.
Cut Residuals, Maximize Clarity
Clean, compliant water doesn’t have to come with excessive chemical use or waste generation. In fact, over-treating can work against you – leaving behind residuals that must be removed later, driving up costs and complicating your process.
Smart programs focus on clean reactions that minimize byproducts. For example, selecting the right scale inhibitor or pH stabilizer for drinking water treatment can reduce the need for post-treatment filtration, saving both energy and filter media. Similarly, using oxidation processes tailored to your target contaminants, like hydrogen peroxide for organic reduction can improve water clarity without overfeeding.
Rethink “Waste” in Wastewater
In many industrial systems, treated effluent isn’t waste but a resource. With the right chemical polishing, treated wastewater can be reused for non-potable applications like cooling tower makeup or process rinse water.
Programs built with reuse in mind focus on reducing organic compounds, controlling bacteria, and eliminating fine particles that cloud up reuse quality. Done right, that means fewer surcharges, less fresh water demand, and a better sustainability profile, all while trimming your total water spend.
Partner With a Formulator, Not Just a Supplier
If you’re serious about optimizing your chemical program, you need more than a catalog and a price sheet, you need a partner who understands the chemistry and the bigger picture. That’s ETI.
We’re not just selling buckets of product. We’re formulating solutions tailored to your exact system, your water profile, and your operational goals. With over 38 years of experience in industrial water treatment, we know how to blend chemistries that cut through complexity and deliver real-world savings.
It’s not about buying the cheapest drum. It’s about getting the right drum – one that helps you:
- Reduce overall chemical volume
- Avoid unnecessary sludge and hauling
- Improve system performance and longevity
- Meet regulatory standards with margin to spare
- Eliminate chemical redundancies and incompatibilities
From chemical precipitation to oxidation systems, from ion exchange to reuse applications, we work with our water treatment partners to design programs that solve problems, not just treat symptoms. And because we’re a chemical formulator, not a water treatment service company, we work behind the scenes to support your success, not compete with it.
If you’re tired of juggling too many products or watching your chemical budget balloon year after year, let’s talk. We’ll help you simplify, and save, without cutting corners where it counts. Contact us today.
FAQs: Fast Answers on Smart Chemical Design
Q1: What’s the biggest cost sink in a typical chemical treatment program?
A: Overdosing and redundancy. Many programs use too much product (or too many products) when a blended or better-targeted solution would do the job more effectively. Poor monitoring and lack of system-specific chemistry are also major contributors to runaway costs.
Q2: How do I know if I’m overdosing or underdosing my system?
A: Consistent monitoring is key. If you’re seeing high residuals, fluctuating system performance, or excessive blowdown, it’s a red flag. Automated feed controls, titration testing, and digital tracking tools can help ensure your dosing matches your actual system demand.
Q3: Can I mix biological and chemical wastewater treatment methods?
A: Absolutely, and in many cases, you should. Biological processes handle organic loading well, while chemical polishing helps fine-tune parameters like metals, turbidity, or residual nutrients. The key is designing them to complement each other, not conflict.
Q4: What kind of ROI can I expect from rethinking my chemical program?
A: While it varies by system, clients often see a 10–30% reduction in chemical costs within the first year, along with lower sludge volumes, improved compliance, and reduced downtime. The biggest ROI? A treatment program that performs reliably without constant firefighting.